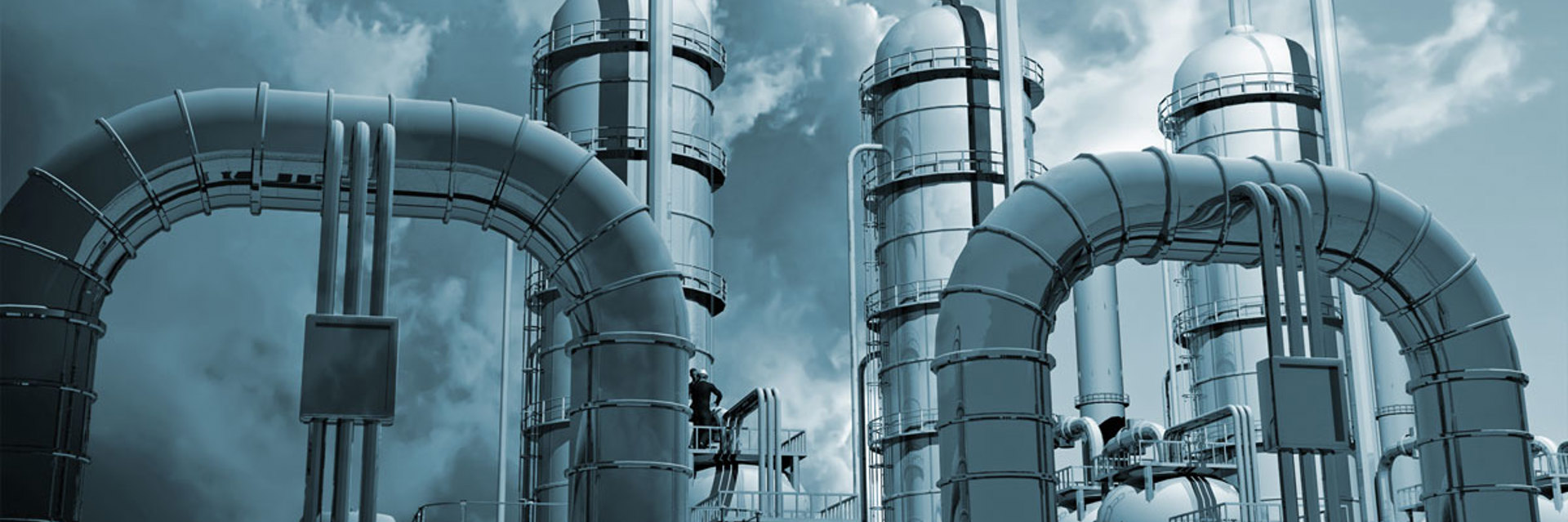
Understanding signal conditioning in industrial automation
In the realm of industrial process control and factory automation, signal conditioning devices play a crucial role in ensuring the accurate transmission of process values. These devices also ensure that the resulting signal is compatible with other equipment interfaces.
Why is signal conditioning necessary?
Output signals from sensors and instruments used in measuring industrial process values are often low amplitude and susceptible to noise and interference.
Without proper signal conditioning, these affected signals may deviate from an accurate representation of the measured value by the time they reach the control system.
Additionally, process signals might be incompatible with interfacing equipment, requiring conversion or modification for seamless connectivity.
What do signal conditioning devices do?
Signal conditioning devices excel at manipulating low amplitude process signals. They can isolate, amplify, filter, convert, split, linearize, and modify signals to ensure a robust and compatible output for connected equipment. Notable examples include signal isolation in high noise/EMC environments, converting signals from thermocouples and encoders, and supplying power for two-wire transmitters.
Typical examples of signal conditioning functionality
- Signal isolation in high noise/EMC environments
- Conversion of the mV signal from a thermocouple into a 4-20mA current signal
- Converting a speed signal from an encoder into a 4-20mA signal
- Converting a resistance output from a level transmitter into 0-10VDC
- Splitting a 4-20mA signal to allow for two identical outputs
- Supplying power for two-wire transmitters
Where are signal conditioning devices installed?
Signal conditioning interfaces are typically positioned between a sensor/measuring point and an input to a control system.
Moreover, these devices play a critical role when strategically positioned between the output of a control system and devices such as valves or actuators. In this crucial position, signal conditioning tailors output signals to precisely match the characteristics required for driving connected output devices. This deliberate placement optimizes communication pathways within the industrial system, providing engineers with the flexibility to fine-tune signal characteristics at pivotal points in the process.
Ultimately, signal conditioning devices act as custodians of signal integrity and reliability, strategically positioned to elevate the efficiency and effectiveness of industrial automation.
Can signal conditioning devices be used for hazardous area applications?
Indeed, signal conditioning is pertinent in hazardous gas and dust applications where process signals are measured in potentially explosive atmospheres. Relevant signal conditioning interfaces are certified based on installation location and chosen protection methods, such as I.S barriers or intrinsically safe galvanic isolators.
Instances where signal conditioning is necessary
- Low Amplitude and Susceptibility to Noise
Challenge:
Output signals from industrial sensors and instruments, such as those measuring temperature, pressure, flow, and level, often start as low amplitude signals.
Issue:
These low amplitude signals are vulnerable to noise and interference during transmission. - Risk of Deviation from Accuracy
Challenge:
In the absence of signal conditioning, these affected signals face the risk of deviating from an accurate representation of the measured value.
Issue:
Noise and interference can distort the original signal, compromising the fidelity of the data that eventually reaches the control system. - Incompatibility with Interfacing Equipment
Challenge:
Process signals, even if accurately measured, may be incompatible with the interfacing equipment of the control system.
Issue:
Without proper conditioning, the control system might struggle to interpret or utilize these signals effectively. - Conversion or Modification for Seamless Connectivity
Challenge:
Incompatible signals require conversion or modification to ensure seamless connectivity with the control system and other equipment.
Issue:
Failure to address this incompatibility could lead to disruptions in the communication between various components of the industrial process. - Ensuring Reliable and Accurate Data Transmission:
Challenge:
The goal is to ensure that the data transmitted from sensors to the control system is reliable, accurate, and free from distortions.
Issue:
Without proper signal conditioning, the integrity of the data is compromised, impacting the overall efficiency and effectiveness of industrial processes.
In summary, signal conditioning is essential to address the inherent challenges associated with low amplitude signals, noise, and potential incompatibilities. It acts as a critical intermediary step, ensuring that the signals maintain accuracy, resist interference, and seamlessly integrate with the broader industrial control system for optimal performance and reliability.
See our range of signal isolators